Tonality for Timber Structures: Low Weight and Minimal Installation Height
They are a perfect match for timber construction: ceramic facades from Tonality. Thanks to the single-layer production – making them particularly lightweight compared to conventional solutions – the required substructure can be significantly reduced. Through the internal insulation, Tonality’s rear-ventilated ceramic facade also minimizes the installation height on the facade – eliminating the need for complex substructures. Timber buildings with Tonality ceramics benefit both from the substantial weight and cost reduction in facade planning and from the excellent fire protection properties and design versatility of the ceramic.
The nationwide timber construction rate has recently increased for both new residential and non-residential buildings. Reasons for this can be found in prefabrication and resource-efficient construction. Tonality, a company belonging to Leipfinger-Bader, has also noticed increasing architect interest in ceramic facades for timber buildings in this context. The decisive factor: the nearly unlimited design possibilities of ceramics and the lifelong product quality. Questions that arise particularly relate to the weight of the ceramic facade. “The weight on the timber facade is an important issue for architects and often causes uncertainties, which can usually be quickly resolved in conversation,” explains Michael Klein, Sales Manager DACH at Tonality (Leipfinger-Bader).
Single-layer, lightweight and environmentally friendly
The single-layer produced Tonality facade ceramic has a low surface weight of only about 40 kilograms per square meter. For comparison: double-layer ceramics weigh about 60 kilograms per square meter or more – making them practically unsuitable for use in timber construction. Despite its single-layer design, Tonality ceramics offer all possibilities for profiling: a profile depth of up to 29 millimeters is easily achievable. A current EPD also certifies that the ceramic facades’ materials and production processes meet the highest sustainability requirements. Phases A1 to A3 (raw materials, transport to factory, manufacturing) account for 18.5 kilograms of CO2 equivalents per square meter. Across phases A1 to A5 (raw materials, transport to factory, manufacturing, transport, installation), it’s 20.95 kilograms of CO2 equivalents per square meter.
Fire protection as a decision factor
The ceramic elements are classified in building material class A1. This means they are non-combustible and naturally contain no combustible components. “More and more planners are choosing ceramic facades for fire protection reasons,” explains Klein. From certain building classes onward, costly sprinkler systems often need to be installed with timber facades. Under certain conditions, these can be omitted when using a ceramic facade. Regional or project-specific fire protection regulations must be considered.
More rentable living space
The rear-ventilated Tonality ceramic facade also ensures a particularly slim wall structure in timber buildings, as the required insulation is located on the inside and the single-layer ceramic has approximately 30 millimeters less installation depth compared to double-layer ceramic panels. This means it doesn’t add extra centimeters to the facade and even saves space. The building thus has more rentable interior space – an important factor especially in boundary development where every centimeter counts. For example, 20 to 24 centimeters of saved insulation thickness can be credited to the interior spaces. High product flexibility is also evident in tolerance management: tolerances from 20 millimeters to 60 millimeters can be easily accommodated. Another advantage: ceramic facades can be completely recycled and remain in the construction industry’s circular economy.
High degree of prefabrication
The system benefits from the advantages of Tonality ceramics, such as free color design, individual designs, and maintenance-free properties. For example, graffiti can be easily removed with conventional cleaning agents. Weather conditions such as heat, cold, rain, snow, or UV radiation damage neither the surface structure nor the color intensity of the ceramic elements, making them a particularly durable, economical solution. And this in many respects: “The system costs remain reasonable. Especially when considering the long-term savings in operating costs, such a device can pay for itself after just two years. In addition, we can offer the renovation of the facade and the integration of the ventilation system as a complete solution. This significantly simplifies planning and implementation,” explains Philip Köthe.
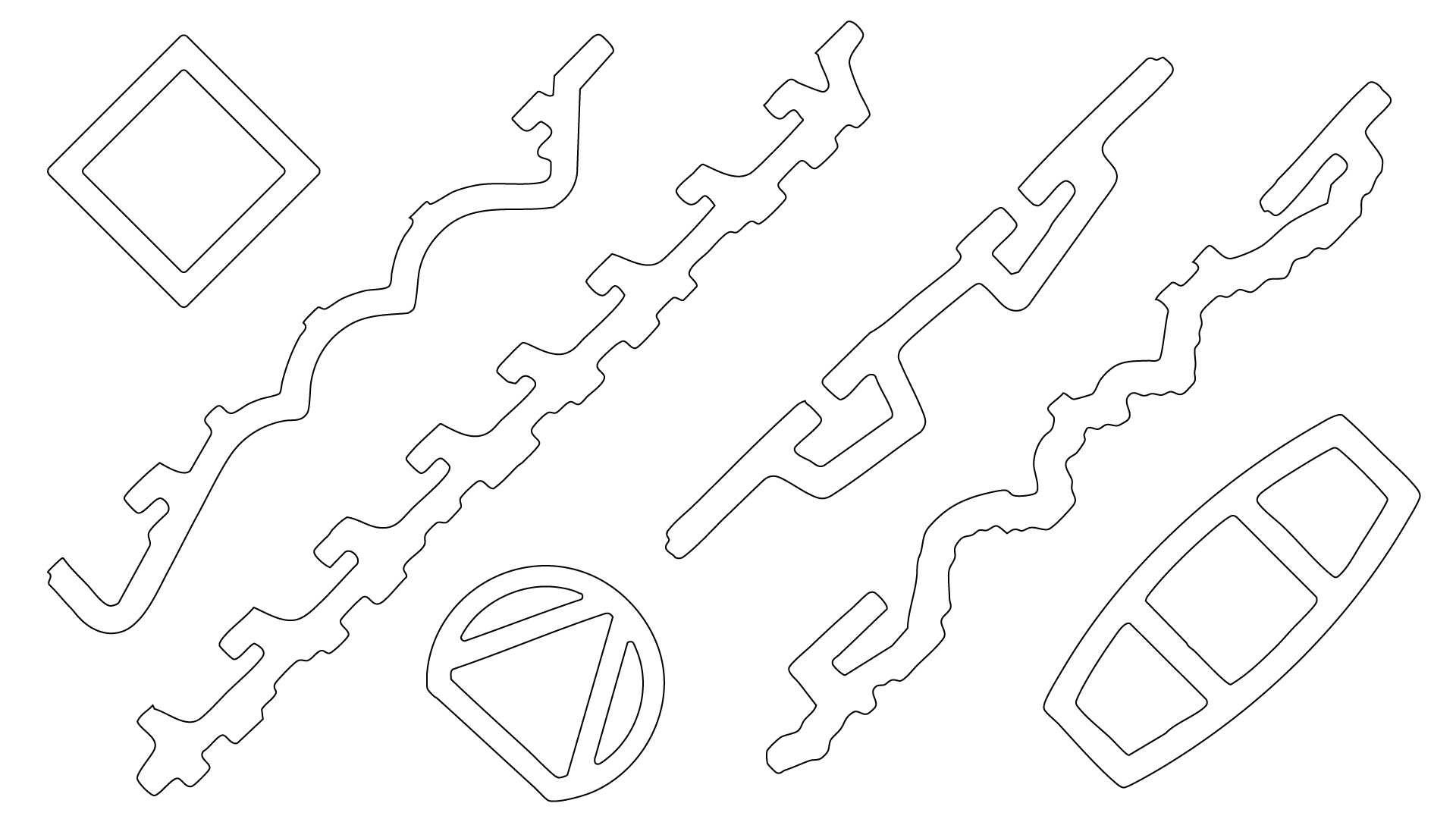
Sustainability and climate protection
In this context, Leipfinger-Bader is also working on increasing the prefabrication level of the ceramic facade for timber construction. For example, it’s conceivable that the substructure could be pre-assembled in the factory and delivered to the construction site as a finished module. There, the ceramic would only need to be hung – developments intended to promote modular construction, relieve skilled workers, and accelerate construction progress.